Material formed from crab shells and trees could replace flexible plastic packaging, research at the Georgia Institute of Technology finds. The new material is made by spraying multiple layers of chitin from crab shells and cellulose from trees to form a flexible film.
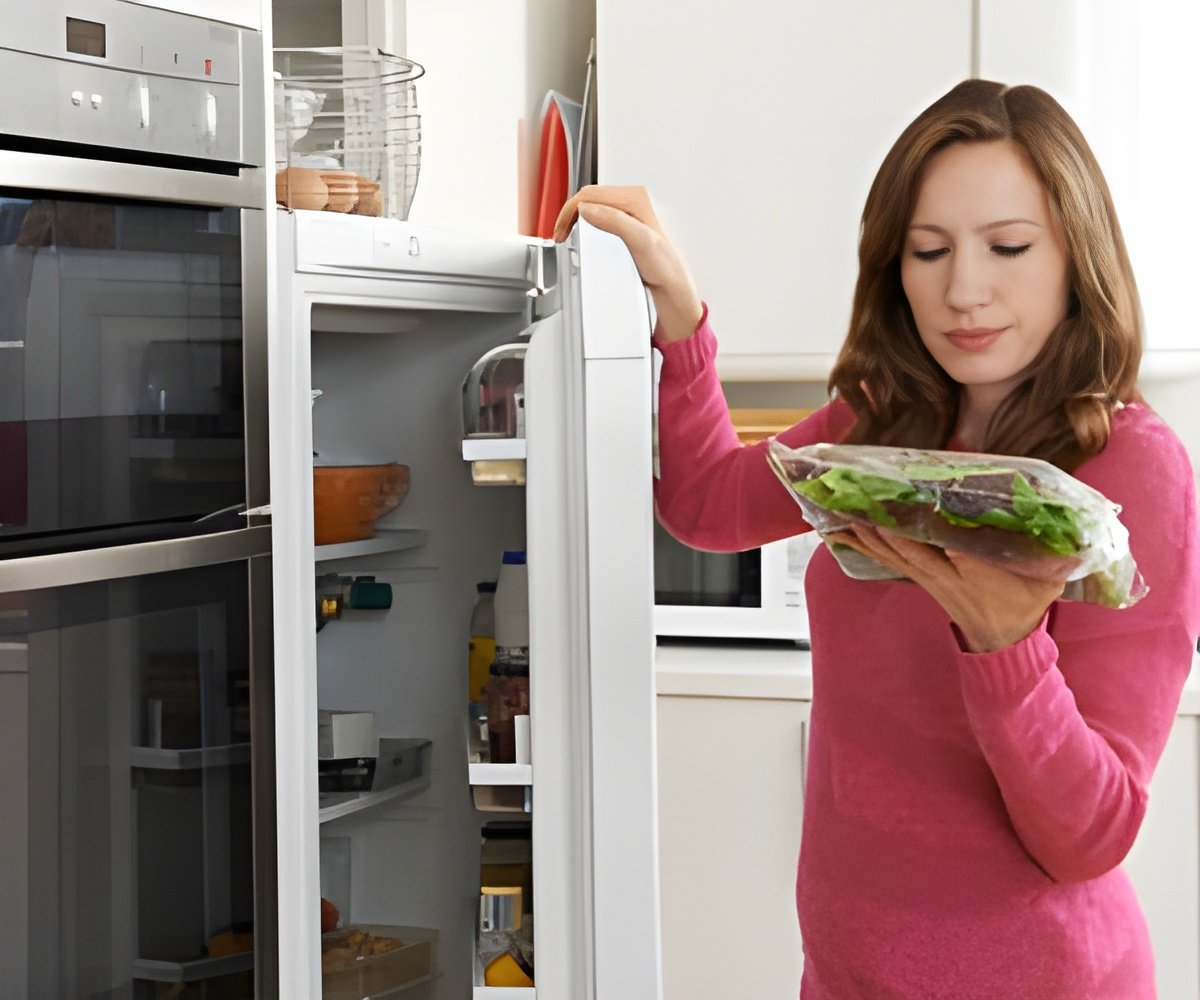
‘A material derived from crab shells and tree fibers that has the potential to replace the flexible plastic packaging used to keep food fresh has been developed at the Georgia Institute of Technology.’
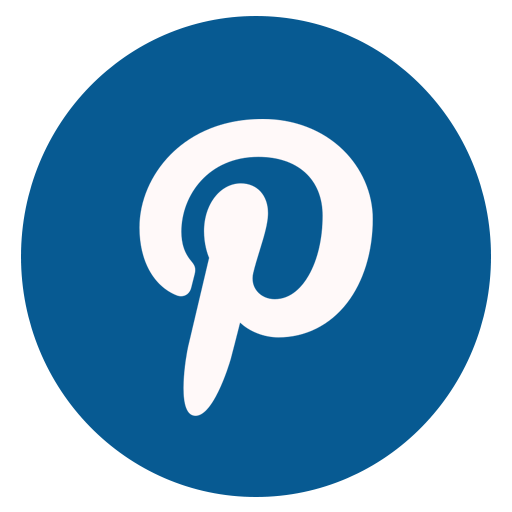
"The main benchmark that we compare it to is PET, or polyethylene terephthalate, one of the most common petroleum-based materials in the transparent packaging you see in vending machines and soft drink bottles," said J. Carson Meredith, a professor in Georgia Tech's School of Chemical and Biomolecular Engineering. "Our material showed up to a 67 percent reduction in oxygen permeability over some forms of PET, which means it could in theory keep foods fresher longer." 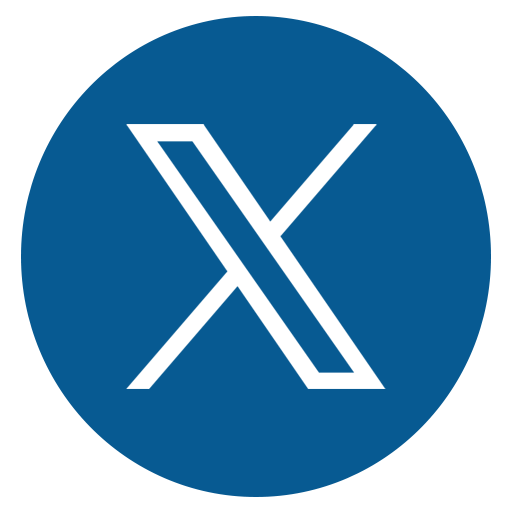
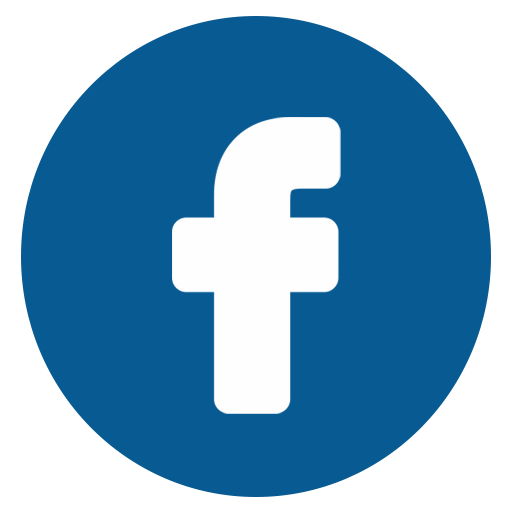
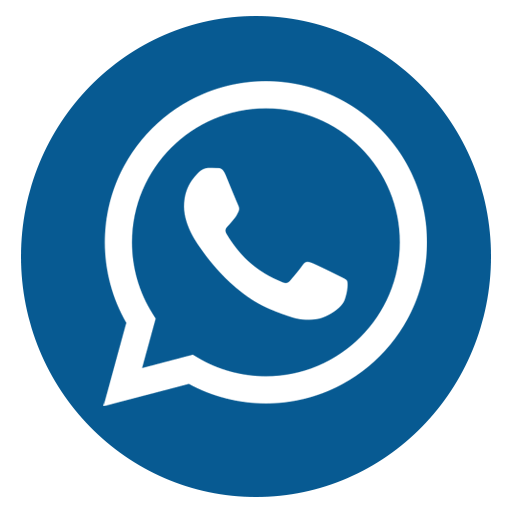
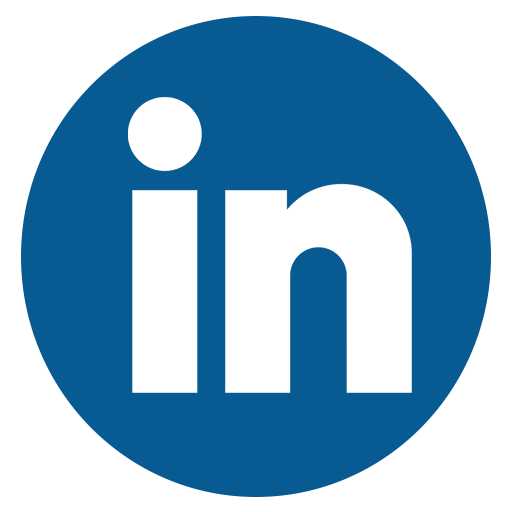
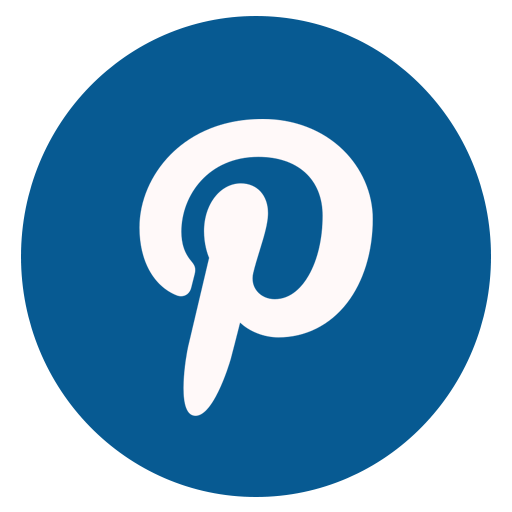
Cellulose, which comes from plants, is the planet's most common natural biopolymer, followed next by chitin, which is found in shellfish, insects and fungi.
The team devised a method to create a film by suspending cellulose and chitin nanofibers in water and spraying them onto a surface in alternating layers. Once fully dried, the material is flexible, strong, transparent and compostable.
"We had been looking at cellulose nanocrystals for several years and exploring ways to improve those for use in lightweight composites as well as food packaging, because of the huge market opportunity for renewable and compostable packaging, and how important food packaging overall is going to be as the population continues to grow," Meredith said.
The research team also included Meisha Shofner, an associate professor in the School of Materials Science and Engineering and the interim executive director of the Renewable Bioproducts Institute, John R. Reynolds, a professor in the schools of Chemistry and Biochemistry and Materials Science and Engineering, and Chinmay Satam, a graduate student at Georgia Tech.
Advertisement
"We recognized that because the chitin nanofibers are positively charged, and the cellulose nanocrystals are negatively charged, they might work well as alternating layers in coatings because they would form a nice interface between them," Meredith said.
Advertisement
"It's difficult for a gas molecule to penetrate a solid crystal, because it has to disrupt the crystal structure," Meredith said. "Something like PET on the other hand has a significant amount of amorphous or non-crystalline content, so there are more paths easier for a small gas molecule to find its way through."
Environmentalists have long looked for renewable ways to replace petroleum-based materials in consumer products. With the amount of cellulose already produced and a ready supply of chitin-rich byproducts left over from the shellfish food industry, there's likely more than enough material available to make the new films a viable flexible-packaging alternative, Meredith said.
Still, there's more work to be done. To make the new material eventually competitive with flexible packaging film on cost, a manufacturing process that maximizes economy of scale will need to be developed. Additionally, while industrial processes to mass produce cellulose are mature, methods to produce chitin are still in their infancy, Meredith said. And, more research is also needed to improve the material's ability to block water vapor.
Source-Eurekalert